Plastic extrusion for creating even, premium parts
A Comprehensive Overview to the Process and Benefits of Plastic Extrusion
In the large world of production, plastic extrusion becomes a vital and highly reliable procedure. Translating raw plastic right into continuous accounts, it accommodates a plethora of industries with its impressive adaptability. This overview intends to illuminate the detailed steps included in this approach, the kinds of plastic appropriate for extrusion, and the game-changing benefits it offers the industry. The following discussion guarantees to unravel the real-world impacts of this transformative procedure.
Understanding the Essentials of Plastic Extrusion
While it might appear complicated at very first glance, the procedure of plastic extrusion is basically easy - plastic extrusion. It is a high-volume production technique in which raw plastic is melted and shaped right into a continual account. The process begins with the feeding of plastic product, in the type of pellets, granules, or powders, right into a warmed barrel. The plastic is after that thawed using a mix of warmth and shear, applied by a rotating screw. Once the molten plastic reaches the end of the barrel, it is forced through a small opening recognized as a die, shaping it into a preferred form. The shaped plastic is then cooled, strengthened, and cut into desired lengths, finishing the process.
The Technical Refine of Plastic Extrusion Explained
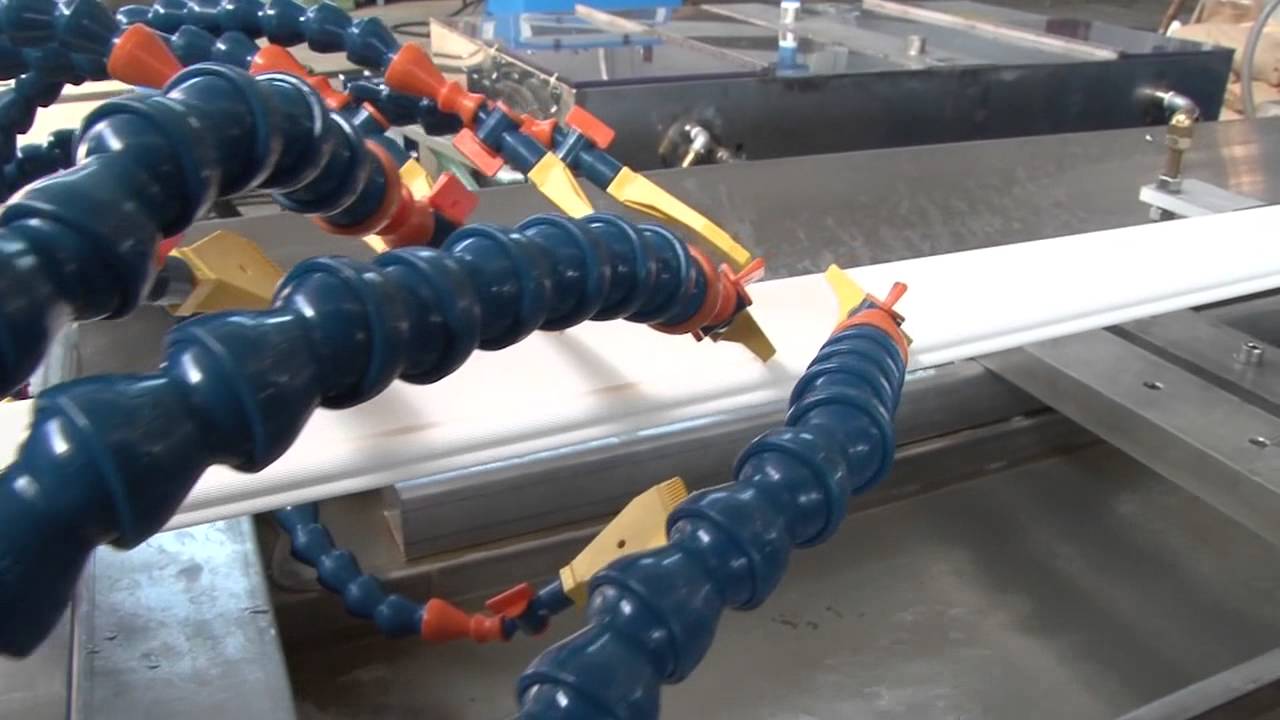
Kinds of Plastic Suitable for Extrusion
The selection of the best type of plastic is a vital facet of the extrusion process. Various plastics provide special homes, making them extra matched to particular applications. Polyethylene, for instance, is typically utilized because of its reduced price and easy formability. It uses outstanding resistance to chemicals and moisture, making it optimal for items like tubes and containers. Likewise, polypropylene is one more preferred choice due to its high melting factor and resistance to exhaustion. For even more durable applications, polystyrene and PVC (polyvinyl chloride) are commonly picked for their stamina and longevity. Although these are usual alternatives, the selection inevitably depends upon the certain demands of the product being produced. So, understanding these plastic kinds can substantially enhance the extrusion process.
Comparing Plastic Extrusion to Various Other Plastic Forming Techniques
Recognizing the kinds of plastic appropriate for extrusion leads the way for a more comprehensive discussion on just how plastic extrusion stacks up versus other plastic creating methods. These consist of shot molding, strike molding, and thermoforming. find more info Each method has its special usages and advantages. Shot molding, for instance, is exceptional for creating complex parts, while strike molding is excellent for hollow objects like bottles. Thermoforming excels at forming superficial or large components. However, plastic extrusion is unequaled when it comes to creating continual profiles, such as seals, pipelines, and gaskets. It also permits a regular cross-section along the length of the item. Hence, the selection of approach mostly relies on the end-product requirements and specifications.
Secret Advantages of Plastic Extrusion in Production
In the world of manufacturing, plastic extrusion provides several substantial advantages. One noteworthy benefit is the cost-effectiveness of the procedure, that makes it a financially attractive production technique. Furthermore, this technique provides exceptional product versatility and enhanced production speed, thereby increasing overall manufacturing efficiency.
Cost-Effective Manufacturing Technique
Plastic extrusion leaps to the forefront as a cost-effective manufacturing technique in manufacturing. This procedure stands apart for its ability to generate high volumes of product quickly and efficiently, giving producers with substantial cost savings. The primary expense benefit is the ability to make use of less costly basic materials. Extrusion utilizes polycarbonate products, which are less costly contrasted to porcelains or metals. Further, the extrusion procedure itself is reasonably easy, minimizing labor costs. Furthermore, plastic extrusion requires less power than standard production methods, contributing to reduced operational expenses. The procedure additionally decreases waste, as any malfunctioning or excess materials can be reused here and reused, supplying an additional layer of cost-effectiveness. Overall, the economic benefits make plastic extrusion an extremely appealing alternative in the production sector.

Superior Item Flexibility
Beyond the cost-effectiveness of plastic extrusion, another significant benefit in making hinge on its premium item versatility. This process permits the development of a broad range of products with varying designs, shapes, and sizes, from basic plastic sheets to intricate accounts. The versatility is credited to the extrusion pass away, which can be personalized to produce the preferred product style. This makes plastic extrusion an optimal service for markets that require customized plastic parts, such as auto, construction, and packaging. The capability to produce varied items is not only beneficial in conference specific market demands but additionally in allowing manufacturers to check out brand-new product lines with marginal funding financial investment. Basically, plastic extrusion's product adaptability fosters development while boosting functional efficiency.
Enhanced Production Speed
A substantial advantage of plastic extrusion lies in its enhanced production rate. Couple of other production procedures can match the rate of plastic extrusion. Furthermore, the ability to keep regular high-speed manufacturing without compromising product top quality sets plastic extrusion apart from various other techniques.
Real-world Applications and Impacts of Plastic Extrusion
In the world of production, the method of plastic extrusion holds profound value. This process is widely made use of in the manufacturing of a variety of items, such as plastic tubing, home window structures, and weather condition stripping. Therefore, it substantially affects industries like construction, packaging, and vehicle markets. Its influence extends to daily items, from plastic bags to toothbrushes and non reusable flatware. The economic benefit of plastic extrusion, largely its cost-effective and high-volume output, has actually transformed production. However, the environmental influence of plastic waste remains a worry. The sector is persistently aiming for advancements in eco-friendly and recyclable materials, suggesting a future where the advantages of plastic extrusion can be kept without endangering environmental sustainability.
Verdict
Finally, plastic extrusion is a efficient and extremely efficient approach of changing basic materials into diverse items. It supplies many advantages over other plastic developing approaches, consisting of cost-effectiveness, high outcome, minimal waste, and layout versatility. Its effect is profoundly really felt in different industries such as construction, auto, and customer goods, making it a crucial procedure in today's manufacturing landscape.
Delving much deeper right into the technical procedure of plastic read this post here extrusion, it begins with the option of the suitable plastic product. Once cooled, the plastic is cut right into the called for sizes or injury onto reels if the item is a plastic film or sheet - plastic extrusion. Contrasting Plastic Extrusion to Various Other Plastic Forming Methods
Understanding the kinds of plastic appropriate for extrusion paves the means for a more comprehensive conversation on exactly how plastic extrusion piles up against other plastic creating approaches. Couple of various other manufacturing processes can match the rate of plastic extrusion.